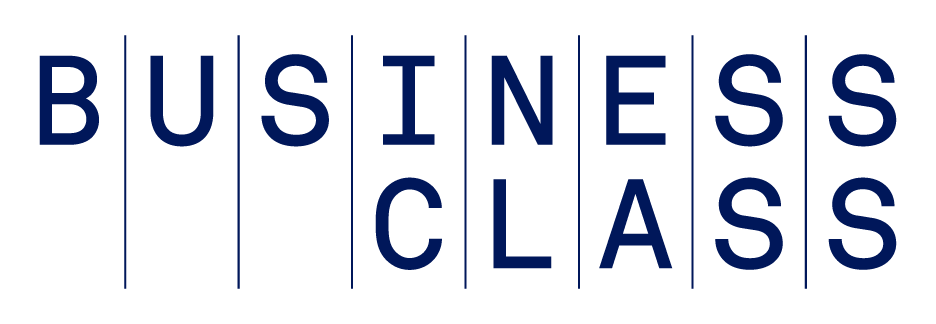
Card Accounts
Business Accounts
Other Accounts and Payments
Personal Cards
Business Credit Cards
Corporate Programs
Gift Cards
Personal Savings
Personal Checking and Loans
Business Banking
Book And Manage Travel
Travel Inspiration
Business Travel
Benefits and Offers
Manage Membership
Business Services
Corporate Programs
Payment Products
Merchant Services